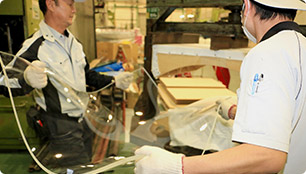
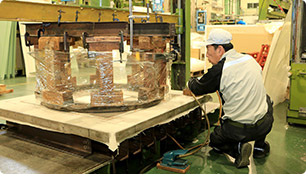
プレス成形とは、プレス機に凸型(オス型)と凹型(メス型)の型を取り付け、加熱軟化させたシート(樹脂板)をその2つの型で挟みこみ(プレス)成形する方法で、樹脂の熱による軟化を利用して曲げる加工方法です。プレス成形は、樹脂への熱伝達が成形方法としては理想的な加工方法に位置づけられ、特に厚板には最適な成形方法です。
また、シート(樹脂板)の周辺をクランプし、内側にエアーを注入して風船のように膨らましてドームを形作るフリーブロー成形があります。形状にもよりますが全く型跡をつけない成形も可能です。これらの技術を生かして多くの水族館で用いられているトンネル水槽(曲面部)も成形することができます。
シンシでは単曲面で最大230mmもの厚板を曲げた実績がございます。シンシの原点となる成形技術です。
- 主な成形型に「木型」と「樹脂型」「金型」とがあり、安価で製作が可能です。(少量多品種に対応)
- 大型成形、厚板成形が可能です。
- 材料をクランプしない場合は、成形による偏肉を少なくできます。
- 型跡が付きにくい。
- 複雑な形状の成形には向いていない。
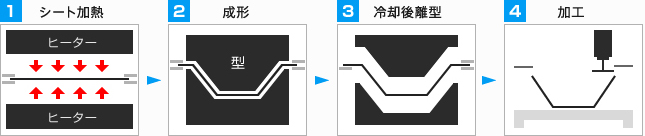
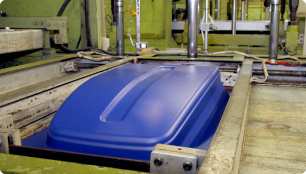
真空成形とは、大気圧をシート(樹脂板)成形に応用した成形方法です。シート(樹脂板)をヒーターにて軟化させ、軟化したシート(樹脂板)と突き上げた成形型との空間(隙間)を真空状態にすることでシート(樹脂板)を型に密着させ、望む形状に仕上げます。
真空成形において、基本成形品の内寸(内側の寸法)が基準寸法となり、凸型(オス型)を用いて成形します。この場合、製品面(型の外側)に型跡が付きません。しかしながら、製品のフォルムは板厚分柔らかく味のあるものに仕上がります。
これとは異なり、インジェクション(射出成形)に近いシャープな成形表現がしたい場合は、大気圧よりも大きな圧力を加える圧空成形が有効です。凹型(メス型)を用いて成形しますので成形品の外寸(外側の寸法)も正確に出ます。但しこの場合、製品面に型が触れますので型跡は避ける事ができません。
型跡に対してはブラスト処理などで対応させて頂いております。また、アンダーカットの成形も可能です。
- 主な成形型に「木型」「ケミカルウッド型(合成木材型)」「樹脂型」「金型」(圧空成形は金型が必要です。)などがあり、型の構造がシンプルで凸型(オス型)凹型(メス型)のどちらか片方のみで成形することができるため、コストダウンに最適です。
- インジェクション(射出成形)と比べた場合、型代が数分の一で済み、小ロット生産に向いています。イニシャルコストの軽減となり、トータルでもお安くなる場合が多いです。
- 成形後のトリミングをNC機械で行っているため、形そのものでなければ型を変更せずに加工プログラムによりカット寸法や穴加工の変更が容易に出来ます。
- 大型成形が可能(最大3000×1500)。但し、成形品の高さに制約があるので注意が必要です。
- 成形後の不要な部分のトリミング作業が必要になり、材料のロスが多くなります。また型当たり面側へのリブ立てなどができない為、接着など二次加工が必要となる場合があります。
- 製品の肉厚が部分的に変動する(元板が伸びた箇所は薄くなる)ため、肉厚調整が困難。
- 製品の表面・裏面のどちらかにしか型に触れない為、寸法精度は型当たり面が基準となります。
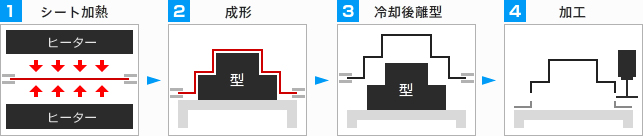
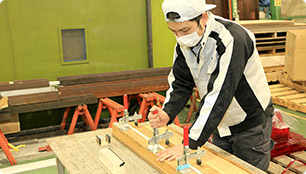
局部曲げとは、シート(樹脂板)を曲げたい部分のみをヒーターなどで加熱して曲げる加工法です。手作業の仕事になり、昔から引き継がれる曲げ技術であり職人の技と呼べる成形方法です。
- 曲げる箇所だけの型で済み、低コストで済む曲げ加工。
- ヒーターで加熱した部分以外に熱による歪みが出ない。
- 直線曲げ加工に限られる。
- 熱をかける箇所とかけない箇所がある為、温度差による反りが発生しやすい。